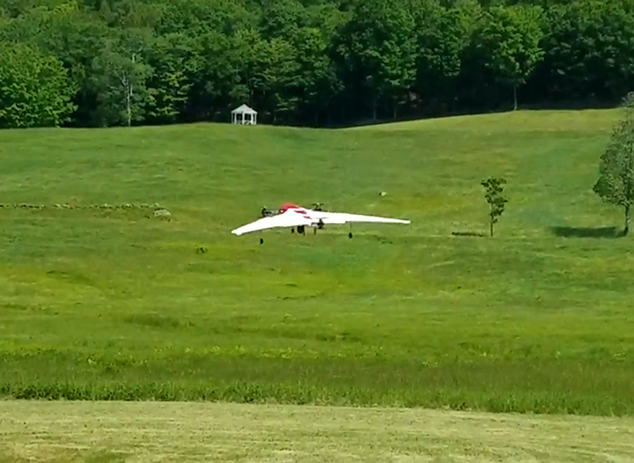
With the backdrop of a perfectly blue sky, I had the opportunity to watch the FireFLY 6 PRO robotic aircraft take flight in a large field and witness it’s capabilities. The aircraft is developed and assembled right here in Andover by a startup company called BirdsEyeView Aerobotics.
In the last few years many types of “drones” have become available for personal and commercial use. Most are “quadcopters” which operate similar to a helicopter. Erich Freymann, a field support rep and factory pilot explained that the Firefly 6 is different than what most people refer to as drone aircraft. It is a fixed wing aircraft with a wingspan of 60 inches that has the ability to take off and land vertically. It is designed to travel at 30 knots which is about 35 miles per hour.
Various “payloads” are available including a variety of cameras for video and still photography. There is also a payload that uses magnets to pickup or drop off loads. Maximum weight of the payload is 1.5 pounds.
Some of the cameras use thermal imaging which can see through smoke and in darkness. This is useful for locating hot spots in wildland fires, and can locate people at times when they would not be visible with the eye or a traditional camera.
Besides search and rescue operations and firefighting, the aircraft is a valuable tool for inspecting power lines and pipelines, creating maps, checking crops and a variety of other tasks.
The fixed wing design gives it a longer range, more speed and longer operating time than most “quadcopters.” It has a flight time of up to one hour depending on wind and payload, and according to the companies website, it can cover up to 600 acres in one flight.
With its ability to take off and land vertically, it can be used almost anywhere that has a 10 foot square open area.
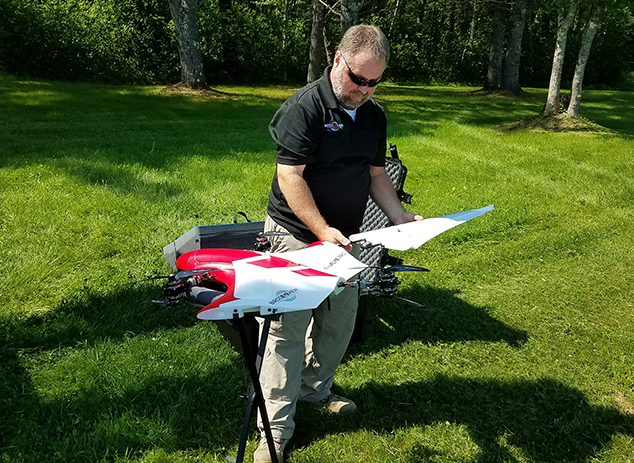
The craft can be operated manually but a flight plan can be programmed in a matter of minutes on a laptop computer and the flight, including take off and landing can be done completely in autopilot. Freymann explained that without vertical take off and landing capability, it is very difficult to make a smooth and safe landing with robotic fixed wing aircraft. Prior to landing the craft during the demo, Freyman had the craft “loiter” which causes it to continuously fly in a 65 meter circle. When the craft was approaching the best alignment to the wind, he then executed the landing.
The Firefly 6 Pro looks like it is made of Styrofoam, but Freymann was quick to tell us that while it may look like styrofoam, it is a very durable and flexible material that holds up very well.
The unit stores away in a large carrying case that will fit in the trunk of most cars. The wings are detachable and held in place by magnets. The landing gear which folds into the wings becomes fully functional once the wing is slid into place. The propellers are also removed for storage. They are easily removed without any tools.
The craft is controlled with a joystick like one you would use with a video game. It interfaces with a laptop computer. The software on the computer accesses available maps such as GoogleEarth for programming flight plans. Maps can be downloaded in advance for use in areas where GPS or internet are not available.
For our demo Freyman set up a flight plan that launched the aircraft and then told it to fly to a house that was across the field. When it reached that location it then circled the house until it was told to execute the next command. The camera on the craft could also be programmed to look at a specific target as it circled. The flight plan then called for the craft to go to other points in the area and to perform different maneuvers. At any time Freymann could shift to manual mode and manoeuver the craft using the joystick.
During part of our demo the camera was switched to thermal imaging mode. People on the ground were instantly visible. Had it been night time, they would still have been plainly visible.
Although the battery powered motors make a lot of noise during take off and landing, once the craft ascended it was barely audible except when right overhead. BirdsEyeView has changed its testing location due to some complaints from residents at their former test area. The new test area provides a large flight area all under the control of a single owner, who has been very supportive.
BirdsEyeView recently received a contract with the U.S. Department of the Interior worth 1.8 million dollars to build up to 50 drones over the next 3 years. These will be used in fighting wildfires and search and rescue operations as well as other scientific missions.
BirdsEyeView Aerobotics was founded by Adam Sloane, who is the Chief Executive Officer, and his wife Christine, who serves as Chief Financial Officer. Adam, who grew up in North Carolina, has degrees in Aerospace Engineering from the University of North Carolina and a MS from Stanford University. After school he worked for a company that was competing for one of the first major portable drone procurements by the US military. He has worked as a defense contractor and designed a couple of small fixed wing drones for military use. After several years as a defense contractor Sloan says “I eventually got frustrated with the military procurement process and the direction in which the technology was being taken (from see-over-the-next-hill reconnaissance applications with a focus on keeping soldiers from walking into danger, to targeting and weaponization). As a result, I left my job in Florida and moved to New Hampshire with the goal of doing something entrepreneurial and a belief that the technology could and should be brought into a form that was accessible and useful to everyday people.”
Sloan’s experience with various robotic aircraft led him to the conclusion that while fixed wing aircraft had many advantages over “quadcopters” and other robotic aircraft that are popular today, they were not practical as “ they require too much space and piloting expertise to safely take off and land in the kind of cluttered environments that the average person encounters on a daily basis. It seemed clear to me that a truly useful flying robot would have to have attributes of both.” Sloan began on the design that would become the FireFLY6 in 2010, and demonstrated proof of concept in 2012. The business began at Sloan’s home office in Sutton, then moved to their barn and eventually to a warehouse in Boscawen.
On his commute to and from Boscawen, Sloan noticed the building at 519 Main Street in Andover and when the sign out front changed from “For Sale” to “For Lease” they quickly moved to secure a space in the building. The components of the FireFly 6 are manufactured elsewhere, but the assembly, and testing takes place in Andover.
The airframe was designed to use motors, propellers and other components designed and manufactured by others. The software that controls the aircraft is developed by an engineer on staff. The design of the aircraft, with it’s vertical take off and landing coupled with software that simplifies the operation and control of the aircraft set the FireFLY 6 apart from other robotic aircraft.
While the FireFLY 6 is designed more for commercial use, Sloan hopes to move toward “bringing the technology into forms that are accessible and useful to everyday people. You’ll see our products continue to evolve towards that over time.” For now, Sloan says that their efforts are focused on improving upon the FireFLY 6 PRO.
Sloan will be offering a public demonstration of the FireFLY 6 PRO during the Andover 4th of July celebration. The demo will take place at Carr Field on Main Street at 10:30 AM.
For more information on the company and their products visit their website: www.birdseyeview.aero.