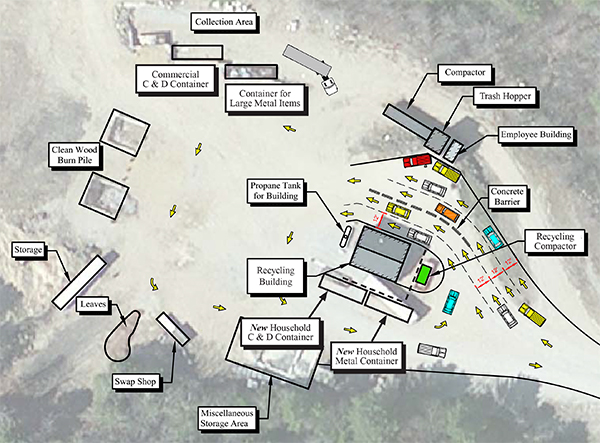
When you visit the Andover Transfer Station, you will see that some major changes are in progress. You will see a new compactor for recyclables; a new four-lane drive-through pattern, with two lanes for recycling and two for trash; and a new barrier between the recycling lanes and the trash lanes. In addition, there were less obvious changes that were needed to configure it all, such as grading, constructing a platform behind the recycling building, and relocating a utility pole.
What drives these changes is an effort to keep the cost of handling the town’s waste materials as low as possible. In addition, we want to recycle or re-use as much waste material as is reasonable, but the market value, labor expenses, and equipment maintenance must be considered when doing that.
Obviously, swings in the economy affect the market value of recyclables, so our Transfer Station needs to be designed to respond to those changes. Currently, given the low market value of recyclables, sorting and bailing recyclables does not make financial sense. It is labor intensive, and our equipment needs to be replaced. So we are currently using the Single Stream Recycling (SSR) approach.
Because the cost of trucking materials is a major part of the cost in handling recyclables, keeping the number of hauls down is critical. Compressed materials require one third the number of hauls as uncompressed materials require, and this is one of the reasons for the new recyclables compactor. The trucking savings alone will pay for the new recyclable compactor in just a few years. Hurray for that!
Another reason for the new compactor is to provide backup in case our current trash compactor breaks down, which would create major problems for the operation.
New Traffic Pattern
There will be a new traffic pattern at the Transfer Station, with two lanes leading past the trash compactor, and two lanes leading past the recyclables compactor and recycling building. Barriers will be set up to guide traffic, and it is expected that a resident with both trash and recyclables to dispose of will make two passes — one through the trash lane, then loop around the recycling building for a second pass, this time through the recyclable lane. This should keep the flow of traffic smooth and efficient, with as little waiting as possible.
We hope that everyone will respect this plan and not carry materials from one side to the other. Use the second pass instead – it’s safer and more efficient.
The new design permits flexibility, so in the future if the market value of recyclables improves, consideration can be given to replacing our two ancient bailers and selecting out some materials from the SSR approach for individual marketing. However, that will be considered in light of the cost of the equipment and labor expense needed, not just the market value of the recyclables.
Developing a flexible design for the Andover Transfer Station has been a real challenge for the Selectmen, but we are very enthusiastic about the new plan. We are very grateful to John Warzocha for his expertise in designing facilities; to our Road Agent, Jon Champagne, and his crew for getting everything done; and to John Elliot of Dumpster Depot for his patience, expertise, and arranging a great deal on the new compactor and containers. In all, a great bunch of people to be working with.